Identifying PFAS in Your Industrial Water Systems
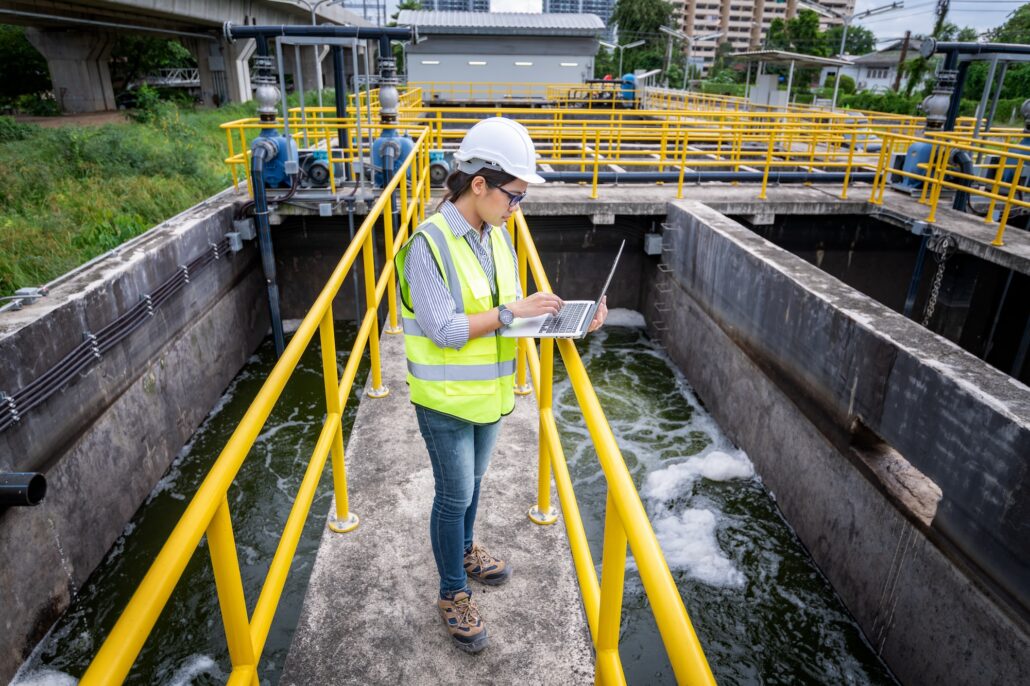
As regulatory agencies intensify their focus on environmental protection, Per- and Polyfluoroalkyl Substances (PFAS) have become a critical concern in water management. This article provides a comprehensive overview of PFAS chemicals, current and emerging water regulations, and practical guidance on how manufacturing facilities can identify sources of PFAS and implement compliant water management strategies.